We want to protect the environment through efficient investments aimed at developing initiatives that limit our environmental impact and promote energy efficiency, responsible resources use and proper waste disposal.
Energy
Energy efficiency and savings are a priority for us and we are committed to gradually improving our energy performance in order to obtain greater efficiency and guarantee the sustainability of our activities.
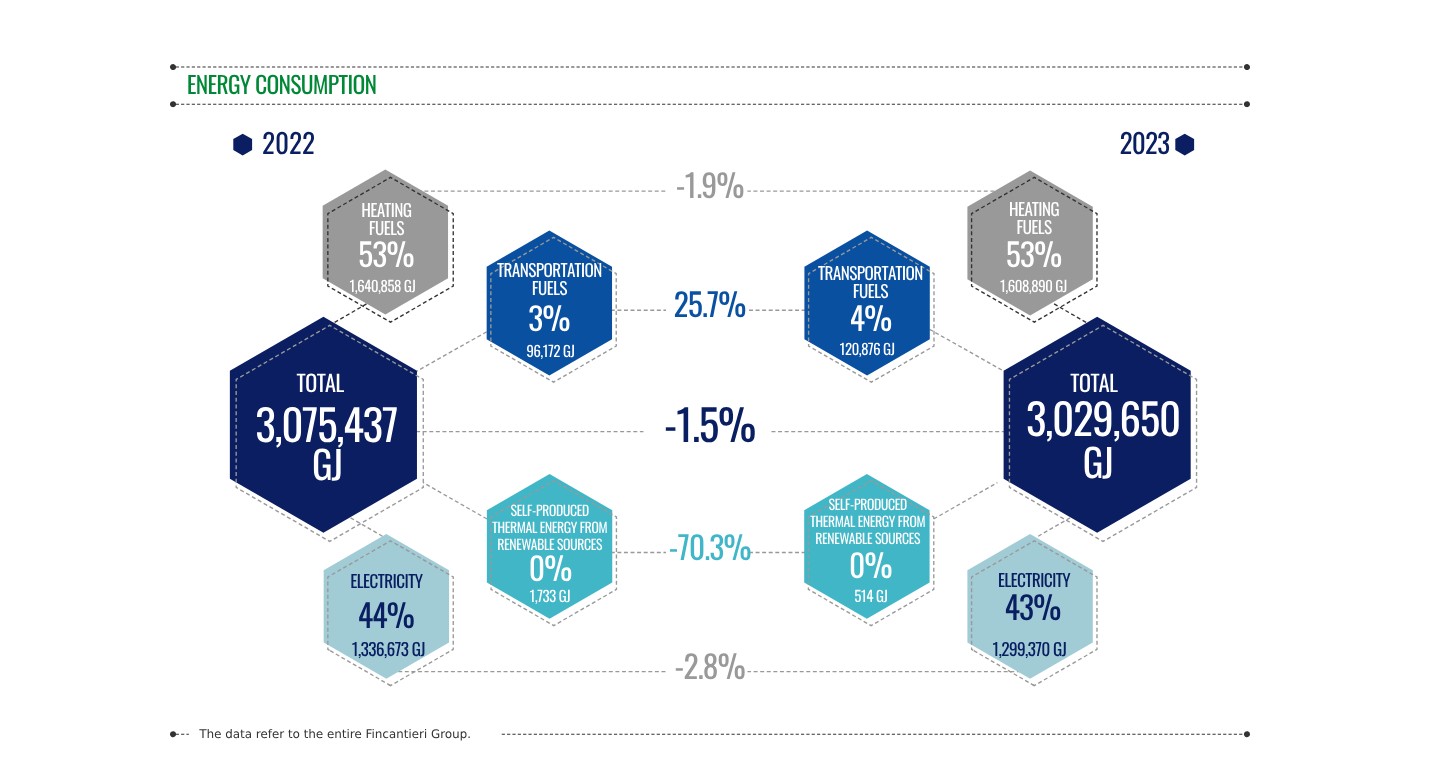
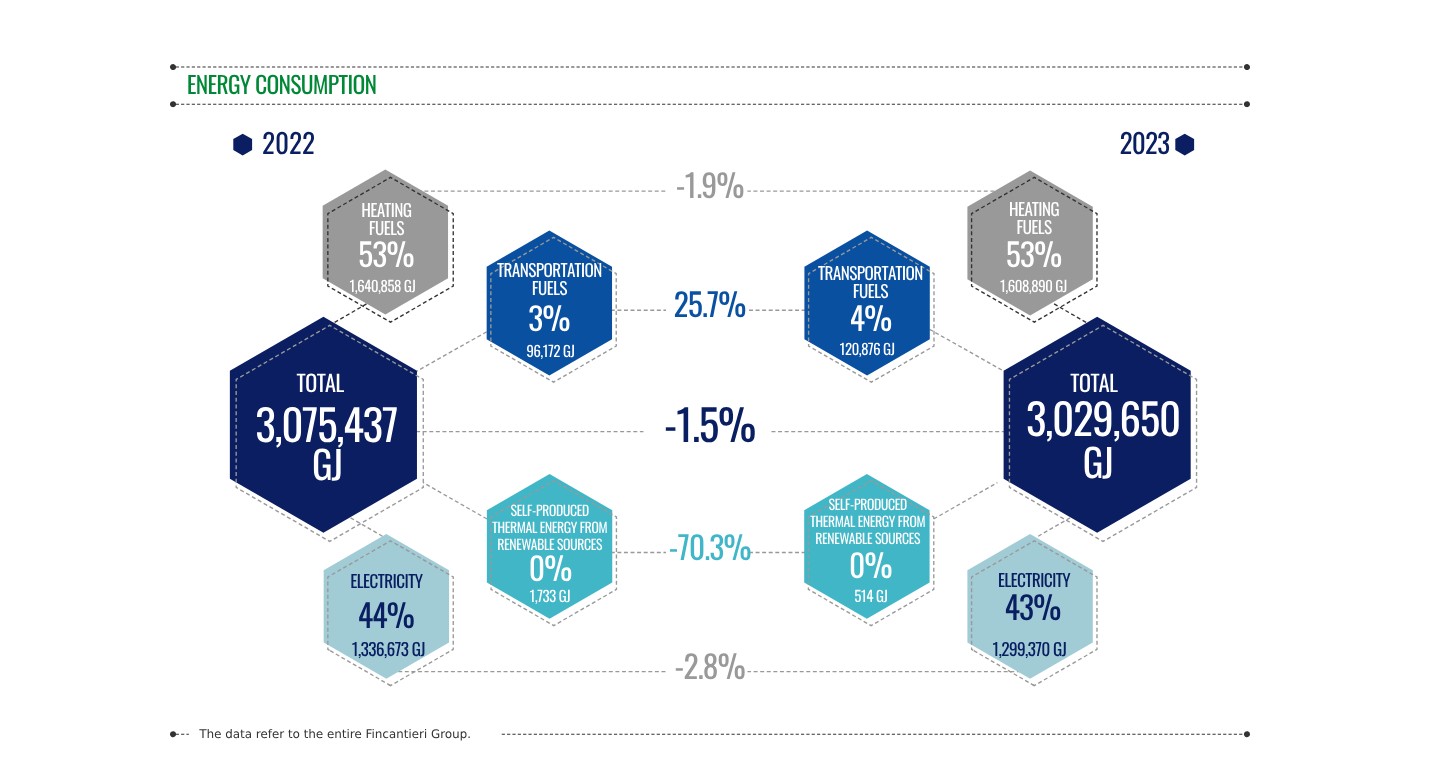
We have established a structure and an organizational process aimed at the preparation of annual site energy diagnosis and the identification of improvement plans aimed at the continuous efficiency of the company’s energy performance. In particular, in our production sites, the replacement of lighting fixtures with new LED technology has continued and systems have been installed for the more advanced electricity and natural gas meters, and automatic switch-off of ventilation, intake and air conditioning systems in Monfalcone were completed.
In 2023, Ancona, Arsenale Triestino, Muggiano and Riva Trigoso shipyards obtained ISO 50001 certification for their Energy Management System, which requires monitoring of consumption and the continuous improvement of shipyard energy performance, while the Monfalcone, Sestri, Marghera, Palermo, and Castellammare di Stabia shipyards have maintained its validity. Important environmental awards have also been achieved in the United States, where Fincantieri Marinette Marine and Fincantieri ACE Marine have manteined Green Marine certification. The largest voluntary environmental certification program.
As defined in the 2023-2027 Sustainability Plan, we set a target aimed at increasing the share of electricity from renewable sources reaching 100% by 2030.
To achieve this goal, Fincantieri signed an agreement with the ESCo (Energy Service Company) Renovit to install photovoltaic systems on several Italian construction sites. The panels already installed have enabled a reduction in electricity withdrawal from the national grid of about 3.5 GWh by 2023. The forecast, after the last panels are fully installed, is to reduce annual electricity withdrawal by about 15 GWh.
In addition, we are committed to purchasing electricity from certified renewable sources with Guarantee of Origin (GO) for Italy, Norway and Romania and with RECs certificates for the United States.
Energy consumption (GJ) | ||
2023 | 2023 % of total | |
Acetylene | 32.737,4 | 1% |
Natural gas | 592.045,2 | 20% |
Diesel | 830.650,0 | 27% |
LPG | 10.748,4 | 0% |
LNG | 8.071,0 | 0% |
Fuel oil | 134.638,6 | 4% |
Total heating fuel energy | 1.608.890 | 53% |
Petrol | 6.187 | 0% |
Diesel | 114.689 | 4% |
Total energy for transport | 120.876 | 4% |
Total thermal energy self-produced | 514 | 0% |
Total electricity | 1.299.370 | 43% |
of which from renewable sources purchased | 1.094.542 | 36% |
of which from renewable sources self-produced | 15.216 | 1% |
Total energy | 3.029.650 | 100% |
The data refer to the entire Fincantieri Group.
Water
In the current context of climate change, the increase in demand for water resources is highlighting how, in a growing number of countries, large quantities of water may no longer be available at low cost.
The efficient management of water and its safeguard are therefore crucial for sustainable development and our sustainability strategy.
Safeguarding water, including through virtuous management of water discharges, is one of the main commitments in our Policy and is also one of the aims of the communication/awareness project, aimed at promoting virtuous and eco-sustainable day-to-day behaviour.
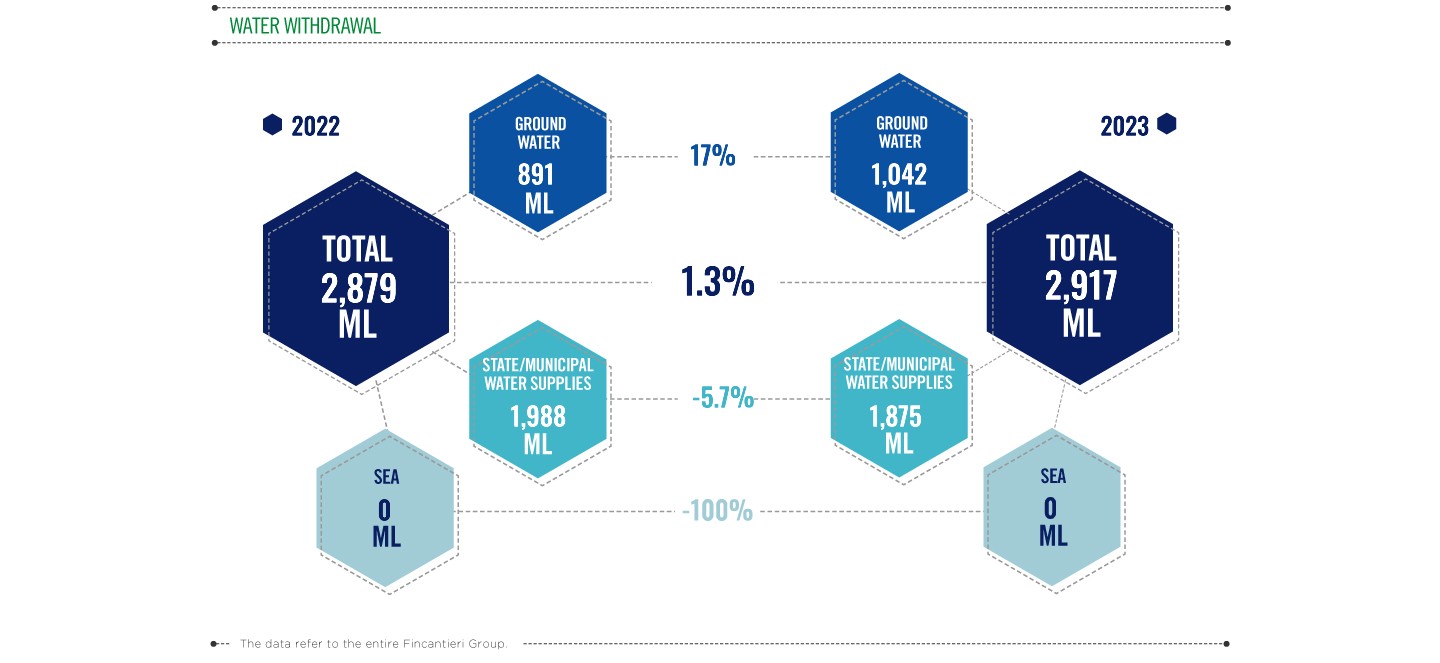
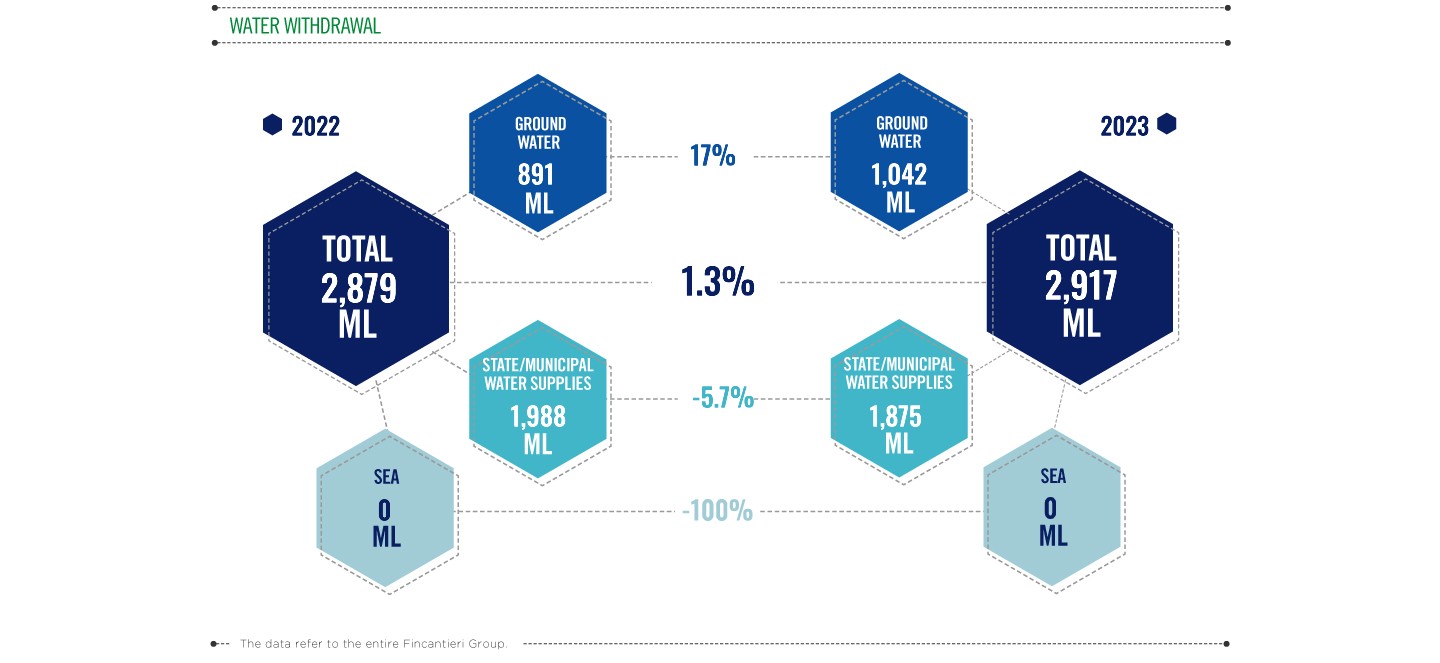
At the level of individual shipyards, as part of the environmental management systems, we continuously oversee the measures implemented to ensure the optimization of water quantity and quality.
We are committed to:
- Implement and maintain our management systems compliant with the ISO 14001 standard;
- Conduct regular monitoring of water withdrawals;
- Monitor water consumption during the production cycle, planning and implementing specific water-saving maintenance actions
- Promote efficient water management practices by minimising fresh water withdrawals, limiting wastewater discharges and minimising losses
- Develop technologies to conserve water;
- Raise awareness among employees and third parties to develop responsible behaviour towards the sustainable use and conservation of water;
- Ensure compliance with applicable local, regional, national and international legislation;
- Develop Group-wide reduction targets.
With reference to the last point, in the Sustainability Plan 2023-2027 we set the following reduction targets at Group level with respect to 2021:
- -3% water withdrawal over hours of production by 2025
- -10% water withdrawal over hours of production by 2027
- -12% water withdrawal over hours of production by 2030
Through the analysis carried out using Aqueduct Water Risk Atlas software, the Ancona, Castellammare di Stabia and Palermo shipyards were found to be within water stress areas and as a result their consumption is particularly stressed.
In order to carry out timely monitoring of water withdrawals in 2023, water meters were installed at the Monfalcone, Ancona, Muggiano and Riva Trigoso shipyards. For the Marghera shipyard, remote monitoring tools of water consumption have been implemented for their timely verification and analysis, while for the Monfalcone shipyard, a verification has been initiated for forms of intervention that can be started as early as 2024.
Raw materials
Procurement of raw materials has a strategic role for our activity. Over the years, we consolidated the process of material selection and procurement, based on which the environmental impact of materials in their entire life cycle is assessed at the design stage.
As per the ecodesign procedure, even while preparing specific contractual techniques, and consequently those needed for the procurement process, we work to identify materials for the interiors that, though possessing the same technical, qualitative and compliance characteristics, are also environmentally compatible.
The main raw materials present in the Group’s production cycle are:
- iron for the hull;
- copper for the electric wiring and automation;
- steel, iron, plastics and other iron and non-iron alloys for the piping installed on board;
- welding materials;
- paint products.
In line with the contents of the Policy regarding the use of chemical products, the supply choices, where there are equivalent technical characteristics and/or compatible performances, continue to be oriented towards products with a lower environmental impact.
In addition, we are committed to the elimination of all products that may contain substances classified as carcinogens, mutagens, or reproductive toxicants (CMRs) by constantly updating our policies.
With regard to paint products, which are quantitatively most present in shipbuilding production, the involvement of suppliers has enabled new low-solvent or water-based products to be introduced into the design specifications.
In pursuing the commitments set out in our Policy, we promote the priority use of materials with lower environmental impact that promote sustainable waste management both during the construction phase of the ship as well as during operation and end of life.
A portion of the steel sheets purchased come from material with a high percentage of recycled steel from scrap. In 2023, we also started, through sales contracts signed by Fincantieri and specialized third-party firms, a virtuous process of recovering steel from scrap from our shipyards.
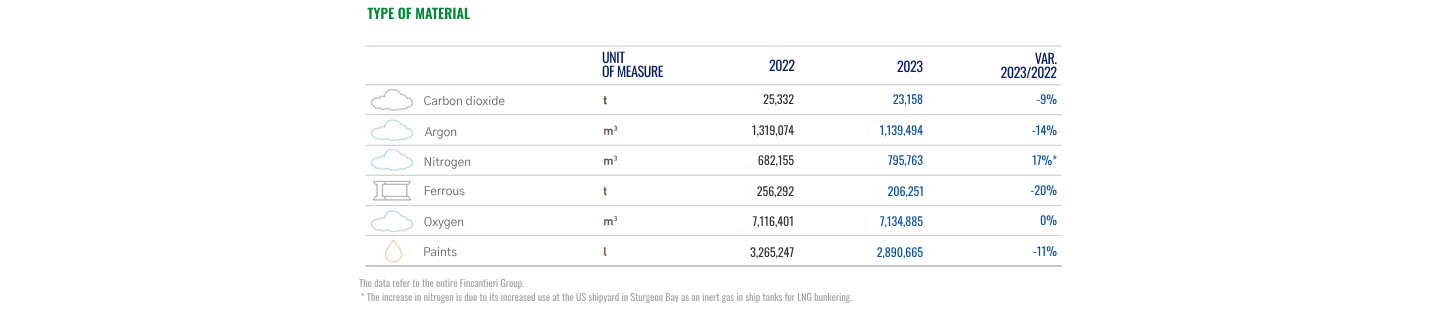
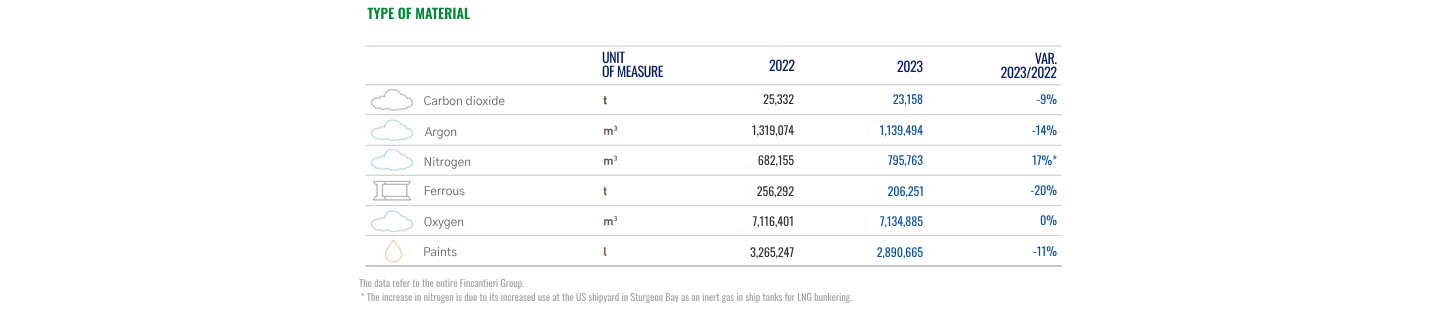
Waste
We promote responsible waste management by strongly emphasizing separate waste collection and reduction especially of hazardous waste.
The criteria identified for managing processing residues and waste disposal are included in the Company guidelines, which are incorporated and detailed in the procedures of each production unit for managing the site’s specificities.
The layout of the production cycle, characterized by specific sequences of the processing phases, makes it possible to optimize the choice and introduction of the materials used upstream and, therefore, to organize the waste sorting and collection methods correctly.
Waste produced by our activities is delivered to authorized sites according to its classification and recovery destinations are favoured and maximized.
In pursuing the commitments set out in our Policy with regard to the supply choices of chemical and paint products, as well as eco-design choices, we promote the use of materials with a lower environmental impact that favour sustainable waste management both during the shipbuilding phase and during operation and end-of-life.
In 2023, the Group successfully diverted 85% of its waste towards recovery, aligning with the targets set in the 2023-2027 Sustainability Plan. This plan aims to maintain an annual recycling rate between 80% and 90% through to 2027. Achieving this milestone was made possible by enhancing waste separation processes across all operational sites. Notably, in Italy, the percentage of waste directed to recovery reached 89%, thanks to targeted policies and effective management of processing residues. A significant aspect of this effort is the management of hazardous waste: in 2023, 63% of hazardous waste was sent for recovery, demonstrating a virtuous and responsible approach.
Given the importance of waste management, the 2023-2027 Sustainability Plan also includes a specific objective to reduce waste generation relative to production hours. The goal is to achieve a 5% reduction by 2025 and a 10% reduction by 2027, compared to 2021 levels.
During 2023, a scouting activity was implemented on a number of initiatives that could be put in place at Italian construction sites to further reduce the waste produced, with a view to the circularity of processing residues. The activities focused mainly on scrap iron and ferrous material scraps with the intention of making them directly available to steel mills in a "furnace-ready" cut for reintroduction into production cycles.
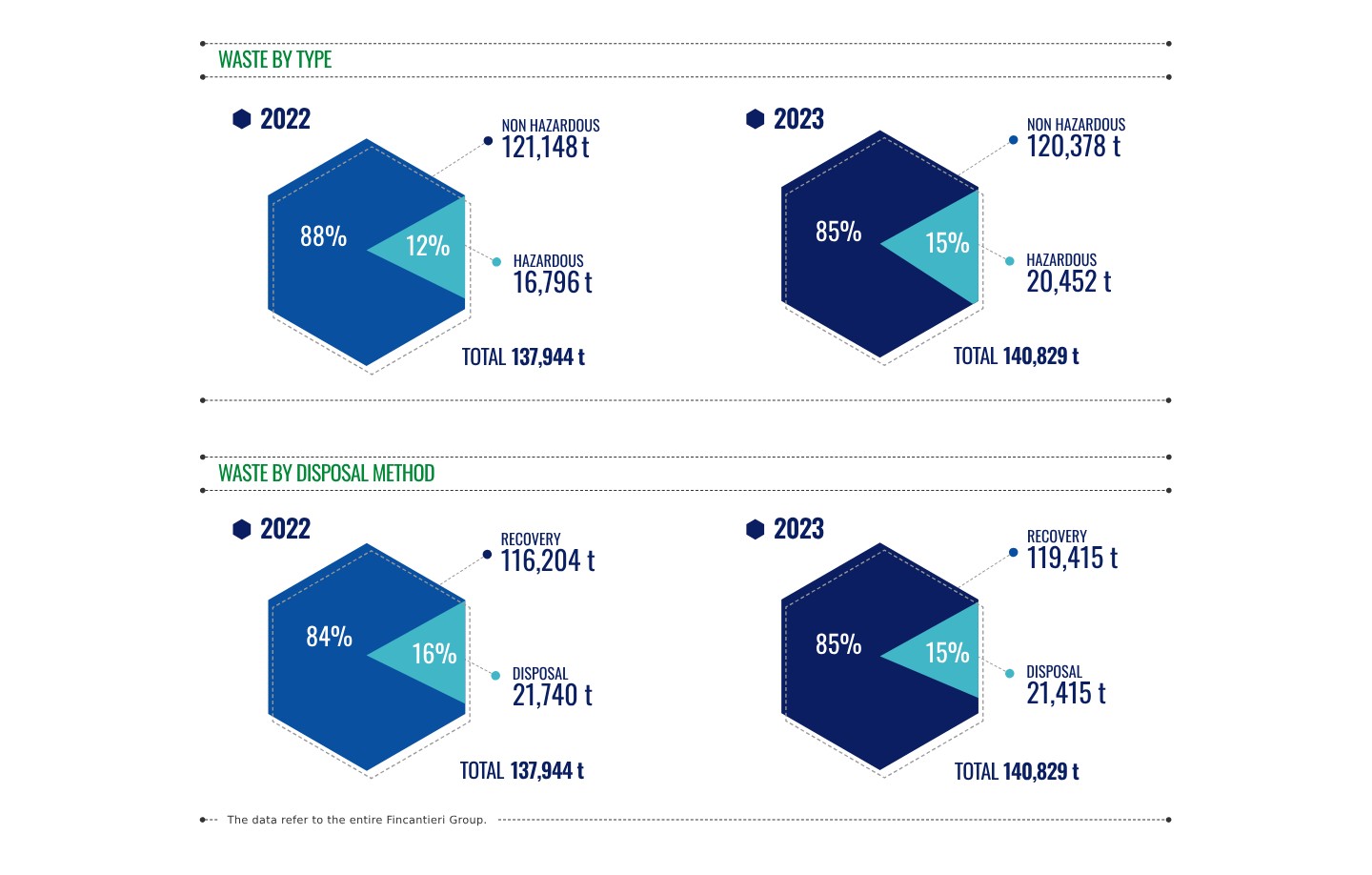
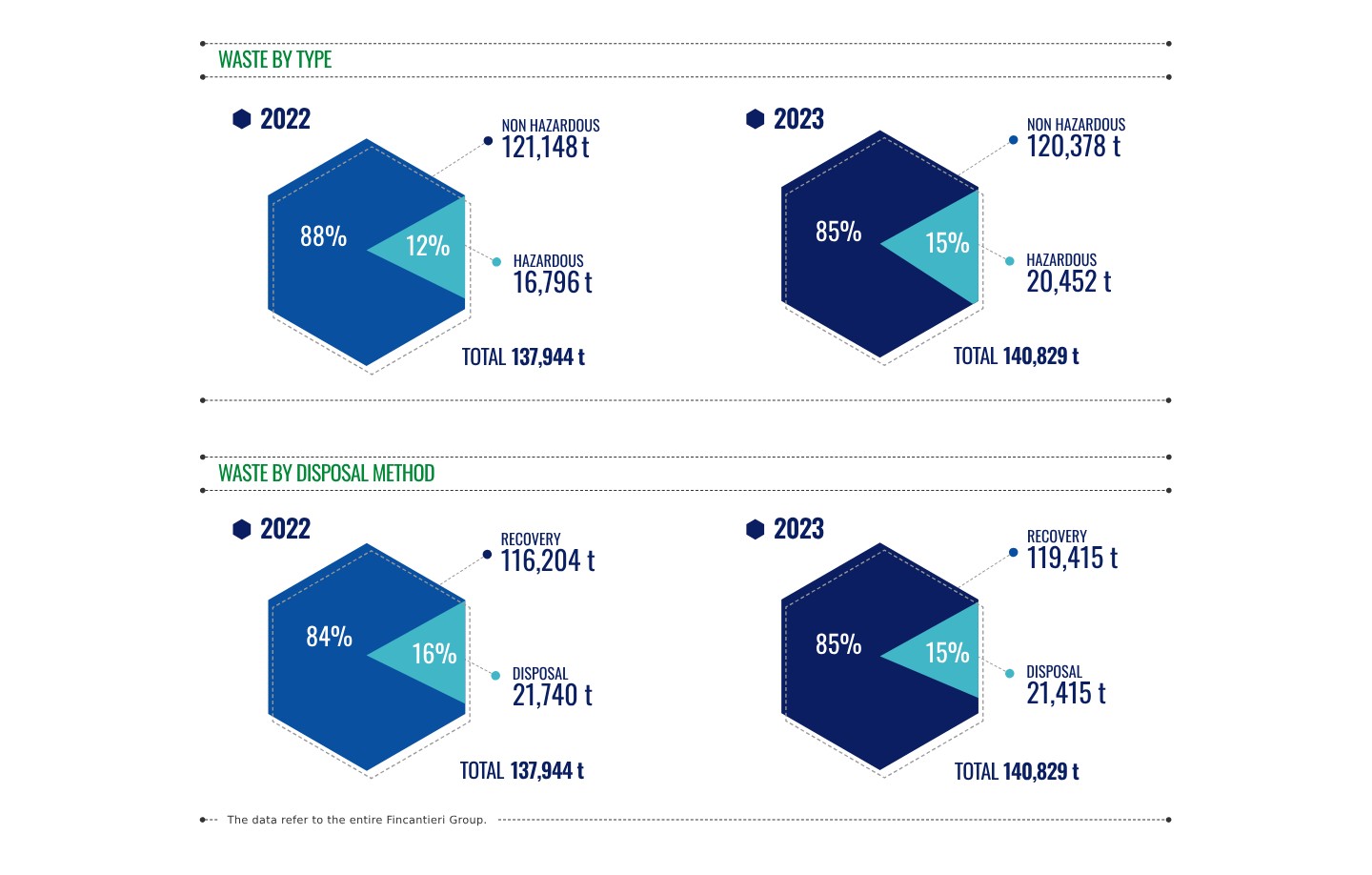
Corporate mobility
We promote a model of sustainable mobility management that concretely affects the reduction of greenhouse gas (GHG) emissions, leading to a change in established habits with a greener perspective.
In Italy a digital company car-pooling service provides and encourages an alternative sustainable solution for employees’ home/work journeys by sharing the use of private cars. The system, also by means of a software application for smartphones or tablets, makes it easy to for employees to get in touch with each other, certify the results in terms of energy and environmental savings and access a reward system that encourages participation in the initiative and helps to change established habits. In parallel, an option has been implemented in the same digital system to certify home/work journeys by bicycle and on foot, and here too access a reward system. Restrictions to contain the spread of COVID-19 have led to a temporary suspension of the car-pooling digital service, scheduled to reopen in 2024.
For business trips, the company policy promotes the use of public transport whenever possible and does not involve excessive travel difficulties, thus limiting the use of cars. With a view to reducing the travel of employees for work, we are also investing in increasingly high-performance technologies that have improved the use and use of video and teleconferencing.
Employees can apply for full or partial reimbursement of their season ticket for urban public transport or train travel, for themselves and/or for their tax-dependent family members through the Welfare Portal.
With a view to sustainable mobility, it is worth mentioning that the various Italian production plants have electric charging stations for the batteries of company vehicles. With regard to the fleet of company cars for business and personal use, as with the fleet of service vehicles, the gradual replacement of current vehicles with hybrid cars, including PHEVs (Plug-in Hybrid Electric Vehicles) is underway. As regards the subsidiaries, both Fincantieri Marine Group and Vard have a travel policy and adopt multiple measures to reduce travel and consequently the impacts.
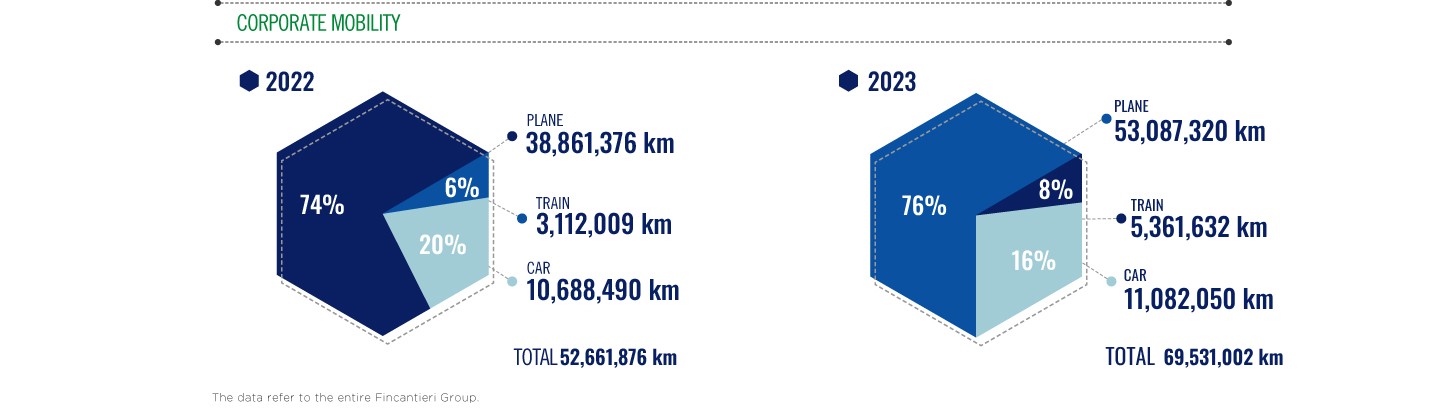
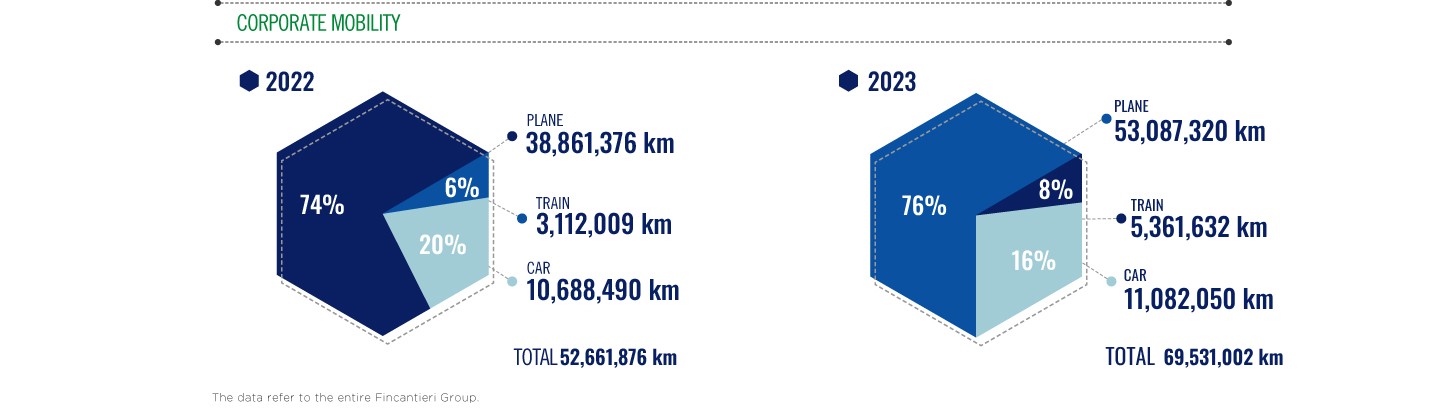
During 2022, business travel increased compared to the previous two years, as, partly due to the vaccination campaign carried out by the institutions and facilitated by the company, restrictions on public transport were progressively reduced/removed (as opposed to restrictions on entry into the various countries).
Greenhouse gas emissions
We are committed to measuring and monitoring the greenhouse gas (GHG) emissions related to our activities in order to verify the effectiveness of the mitigation strategies implemented by the Group and to demonstrate our commitment in the fight against climate change.
In 2023, our total greenhouse gas (GHG) footprint from direct emissions from sources owned by or under the control of the Group (Scope 1), indirect emissions from electricity consumption (Scope 2) and other supply-chain indirect emission (Scope 3) amounted to more than 22 million tonnes of carbon dioxide equivalent (tCO2e).
A specific target to reduce GHG emissions from Scope 1 and 2 compared to 2021 was included in the Sustainability Plan 2023-2027, with targets of -4% in 2025, -8% in 2027 and 20% in 2030 compared to 2021.
In 2023 we have reduced, thanks to energy efficiency measures such as relamping, total emissions from Scope 1 and 2 calculated according to the marked-based medoto by more than 4%.
In line with our aim to play a leading role in decarbonizing the shipping sector, during 2023 we expanded our reporting of emissions from Scope 3 to include CO2 emissions from the "End of life Traetment of Sold Products" as required by the Greenhouse Gas Protocol reporting standard.
SCOPE OF EMISSIONS [TONS OF CO2e] | 2022* | 2023 | VAR 2023/2022 |
SCOPE 1 | 118,461 | 118,984 | 0.4% |
SCOPE 2 | 32,653 | 25,975 | -20.5% |
Electric energy (Location-Based) | 112,204 | 106,877 | -4.75% |
Electric energy (Market-Based) | 32,653 | 25,975 | -20.5% |
SCOPE 3 (EXCLUDING «USE OF SOLD PRODUCTS») | 1,130,248 | 1,202,688 | -7.4% |
Cat. 1 Purchased goods and services | 997,708 | 1,036,342 | -9.6% |
Cat. 2 Capital goods | 56,186 | 70,158 | 24.9% |
Cat. 3 Fuel- and energy-related activities (not included in scope 1 or scope 2) | 30,866 | 30,588 | -7.0% |
Cat. 4 Upstream transportation and distribution | 25,280 | 27,698 | 9.6% |
Cat. 5 Waste | 6,707 | 7,258 | 8.2% |
Cat. 6 Business travel | 5,548 | 8,110 | 46.2% |
Cat. 7 Employee commuting | 7,526 | 7,564 | 0.5% |
Cat. 12 End of life Traetment of Sold Products | 17,676 | 14,455 | -18.2% |
Other (water withdrawal) | 429 | 515 | 20.3% |
TOTAL SCOPE 1+2+3 (EXCLUDING «USE OF SOLD PRODUCTS») | 1,449,871 | 1,347,647 | -7.1% |
Cat. 11 Use of sold products | 21,798,611 | 21,173,247 | -2.9% |
TOTAL SCOPE 1+2+3 | 23,248,481 | 22,520,895 | -3.1% |
The data refer to the entire Fincantieri Group.
*The 2022 Scope 3 figures have been reclassified for comparative purposes following the expansion of the reporting (inclusion of VARD ships in Cat.1 and introduction of Cat.12 ‘End-of-life treatment of sold products’; the contribution of electricity transport from renewable sources has been added to Scope 3. The estimates follow the recommendations of the Corporate Value Chain (Scope 3) Standard of the GHG Protocol.
Perimeter and calculation methods:
• Cat.1 – the data refer to the purchase of goods for the production of the Group’s ships. For each ship under construction, the carbon footprint from the materials used was calculated and the annual emission was broken down according to the percentage of cost associated with each order.
• Cat.2 – the data refer to the entire Fincantieri Group.
• Cat.3 – the data refer to the entire Fincantieri Group.
• Cat.4 – the data include the procurement of raw materials by Fincantieri S.p.A. and Fincantieri Marine Group and the internal handling of Fincantieri S.p.A. and VARD ship sections.
• Cat.5 – the data refer to the entire Fincantieri Group.
• Cat.6 – the data refer to the entire Fincantieri Group.
• Cat.7 – the data refer to employees and blue collar workers of Fincantieri S.p.A.
• Cat.11 – the data refer to emissions from the operational phase of ships delivered by the Fincantieri Group. Each type of ship (cruise, naval, specialized) was associated with an operational profile and a useful life for estimating emissions at sea and in port.
• Cat.12 – the data refer to emissions from the disposal phase after the lifecyle of the ship delivered by the Fincantieri Group. For each ship, the emission was estimated based on the carbon footprint of its components during the disposal phase.
• Other – the data refer to the entire Fincantieri Group.
Demonstrating the Group's commitment to fight climate change, since 2016 we have joined the Climate Change Program of CDP whose goal is to improve environmental risk management by leveraging information transparency. The Group on the occasion of the annual data collection by CDP drafts the Greenhouse Gas Statement, a document containing detailed information on Scope 1, Scope 2 and Scope 3 emissions. The document has been subjected to conformity assessment according to the criteria indicated by the "International Standard on Assurance Engagements 3410, Assurance Engagements on Greenhouse Gas Statements" ("ISAE 3410") by the independent auditing firm Deloitte&Touche S.p.A, which expresses on the basis of a Limited Assurance, in a separate report, an attestation regarding the conformity of the information provided.
Other emissions of polluting gases
We are also committed to reducing other polluting gas emissions. For this reason we have activated a monitoring and timely reporting system for certain polluting gases.


The conversion of most thermal plants in Italian factories has involved the elimination of heavy fuels and the introduction of methane plants, resulting in negligible emissions of sulfur oxides (SOx).
With a view to continuous improvement, the VARD group continues to research new approaches to contain and minimize the impact of emissions resulting from industrial activities. The group's commitment is also demonstrated by its participation, since 2008, in the Confederation of Norwegian Enterprises' NOx-Fund, whose primary objective is to reduce emissions of NOx.
A specific Volatile Organic Compounds (VOC) reduction target on production hours was included in the Sustainability Plan 2023-2027 with targets of -3% in 2025 and -5% in 2027 compared to 2021.
Compared to 2021, the baseline of the Plan target, VOC emissions have decreased due to initiatives taken to replace traditional paint products with low-solvent or water-based solutions. These initiatives cross-sectorally involved suppliers, factories, and shipowning companies involved in construction underway. The increase in activities developed within facilities equipped with high-performance abatement conveyance systems also had a significant impact.


Environmental investments
In 2023, we invested 5.7 million euros in environmental protection.
In particular, the Parent Company has consolidated its commitment to implementing initiatives aimed at continuous improvement regarding the impact on all environmental compartments. The main ones regarded:
- The optimization of energy consumption;
- The introduction of tools for monitoring water consumption and reducing waste;
- The improvement of its flue gas extraction systems;
- The improvement of plant process water capture facilities;
- The reduction of noise pollution;
- The continuation of management and plant engineering activities to align standards with the requirements of environmental permits (AIA and AUA).