Occupational safety, workers' health, care and improvement of working environments have always been our guiding principles and the basis of our policies, which consider safety as a strategic and development factor of the enterprise. We place strict protection of the health and safety of all workers, whether they are our own employees or those of contracting companies, at the basis of every action.
We have integrated these commitments into our governance by implementing an Integrated Management System of Health and Safety at Work, Environment and Energy, whose Policy - approved by the CEO of Fincantieri S.p.A, binding for all Group employees and addressed to the entire supplier base - is shared through the coordination activities carried out in the different production units.
At the strategic level, bringing a zero-injury future on board is one of our priority goals and achieving zero injuries our course. With this ambition we launched the Safety Improvement Plan in 2023.
Included in the Plan is the Zero Accidents Future On Board #SAFETYONBOARD institutional communication campaign. Inaugurated on April 28, 2023 on World Occupational Safety and Health Day, the campaign raises awareness of the importance of keeping our people focused, through billboards, digital signage and experiential activities at construction sites.
Watch the video
As part of the Plan, other initiatives have also been launched, all aimed at spreading a culture of safety and promoting a dialogue on the subject. These initiatives are in continuity with, and reinforce, the activities envisaged by the Memorandum of Understanding signed between Fincantieri S.p.A. and INAIL (National Institute for Insurance against Accidents at Work).
Some of the main initiatives planned in the field of Occupational Health and Safety can be explored below.
HEALTH AND SAFETY MANAGEMENT SYSTEM
To ensure optimal management of Occupational Health and Safety, we adopt best practices in this area and have Management Systems in place for all Group sites. For these Management Systems, moreover, we have obtained certification according to the ISO 45001 standard in relation to 100% of Italian production sites and 89% at the Group level.
The Management Systems enable us to:
- carefully analyze all risks to the health and safety of our employees and suppliers;
- Structure appropriate prevention and protection measures to eliminate or minimize these risks;
- Systematically disseminate training and information about Occupational Health and Safety.
Over the years, these measures have produced a steady improvement in performance in this area, steadily reducing injury cases.
RISKS MANAGEMENT AND HEALTH MONITORING
We constantly monitor the health risk elements of our people through appropriate health surveillance that, within the protocols, includes:
- Periodic medical examinations;
- Specialist assessments;
- Diagnostic examinations.
Based on the results obtained from these activities, we take specific measures to prevent, protect and promote the well-being of all workers.
Also with this in mind, we conduct meetings at each site with employees and Workers' Safety Representatives. The meetings are also aimed at identifying possible sources of work-related stress. Upstream of these meetings, initiatives can be defined, where necessary, in logic of risk reduction, for example through specific training courses or organizational measures.
ACCIDENT PREVENTION AND CONTROL
We are committed to ensuring continuous improvement in Health and Safety performance, particularly in relation to the occurrence of accident incidents.
To control and prevent accidents, we carry out technical analyses and investigations, both at the Group and site levels, about the trend of the accident index related to employees and contracted firms and individual events that resulted in an accident, as well as near misses. The results of the analyses and investigations are summarized in reports to the various levels of responsibility and to top management and lead to the implementation of corrective actions.
Prevention of accident events also takes place through a culture of dialogue and collaboration. With this in mind, monthly corporate coordination meetings are held involving all those involved in the governance of Occupational Health and Safety, i.e., HSE managers, those responsible for prevention and protection services (RSPP), the managers of each production site and the main Italian subsidiaries, and the Directors and HR Business Partners of the individual plants.
A guiding tool for prevention is then the Accident, Near Miss, Unsafe Condition/Behaviour and Positive Feedback Management Procedure, updated in 2023, which establishes how to make detections of accident and similar incidents. To ensure the effectiveness of the Procedure we have implemented a digital medium, which allows in relation to each incident the recording and management of Unsafe Observations, the archiving of photographic evidence and the indication of the corrective measures implemented.
Finally, we ensure a healthy and safe working environment by raising awareness of this issue among our top management. For them, we have also adopted specific Health and Safety targets to determine the variable compensation of figures with managerial and supervisory roles.
Our performance on Health and Safety testifies to the effectiveness of the measures described above.
HEALTH AND SAFETY INDICATORS
2017 | 2018 | 2019 | 2020 | 2021 | 2022 | 2023 | |
Number of recordable work-related injuries | 343 | 301 | 339 | 254 | 265 | 296 | 245 |
Frequency rate (injury rate) (LTIFR) | 9.4 | 8.5 | 9.7 | 7.7 | 7.4 | 8.1 | 6,6 |
Severity index (LTSR) | 0.3 | 0.3 | 0.2 | 0.2 | 0.2 | 0.3 | 0,2 |
The data refer to the entire Fincantieri Group.
Index Frequency Rate (LTIFR), i.e. considering the sum of injuries at work with at least one lost working day.
The severity index was calculated as: (number of days lost due to injury/hours worked) * 1,000. and was evaluated as the Lost Time Severity Rate (LTSR), i.e. taking into account the number of days of absence due to injury, starting from the first day after the injury.
TRAINING, INFORMATION AND PREVENTION
We believe that spreading the culture of Occupational Health and Safety is a fundamental preventive measure. Therefore, we constantly invest in training and informing our employees, offering them comprehensive and up-to-date programs covering a wide range of topics.
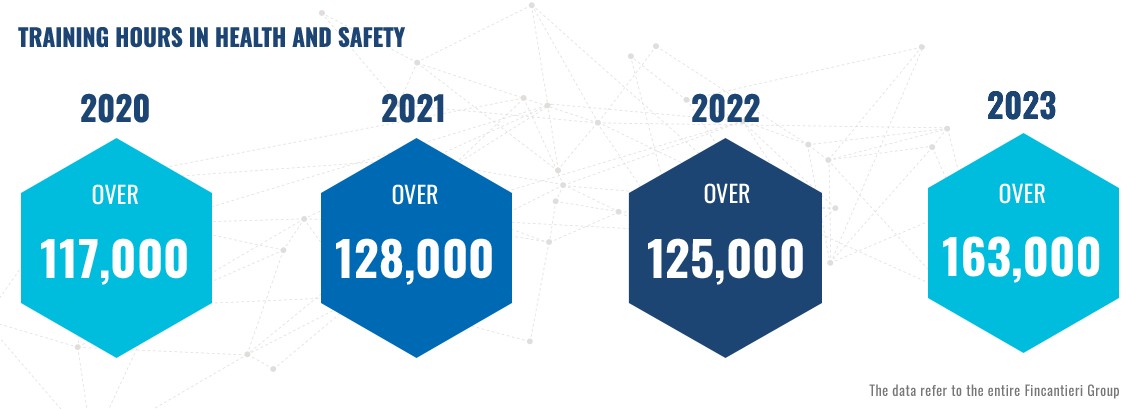
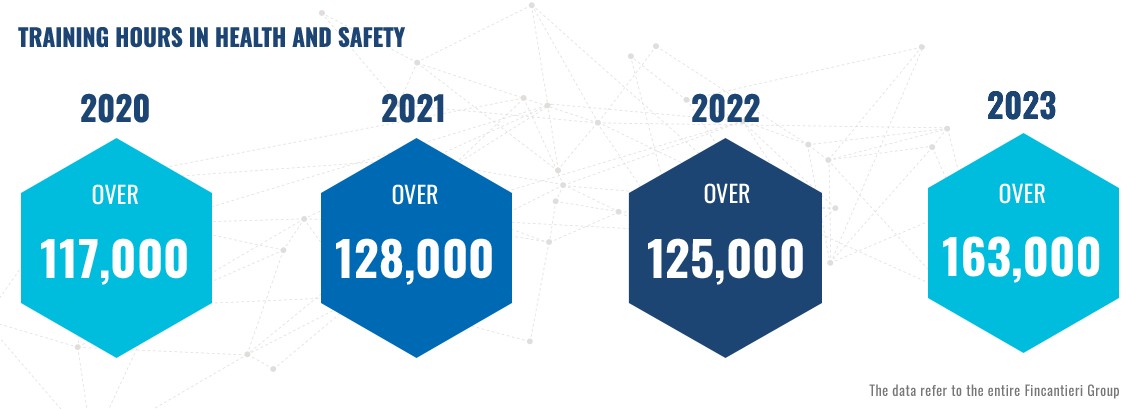
Watch the video
Copyright
This video and its content such as, but not limited to, text, design, audio and images are the property of FINCANTIERI S.p.A and cannot be used, copied, downloaded, published, sent, forwarded or circulated without the prior written approval of FINCANTIERI S.p.A.
Which objectives do we have on this topic?
Health and safety in the workplace: 2023-2027 Sustainability Plan objectives and targets
Continuous improvement of workers’ health and safety conditions
Discover the objectives
Improvement of health and safety at work performance with a view to zero accidents to protect workers' health and the work environment
Description/Target | Ttimeline | Perimeter | Status | SDGs |
Contain the frequency rate for work-related injuries* below 7.5 for the next 5 years
* Frequency rate (injury rate) (no. of work-related injuries/hours worked x 1,000,000) |
2023-2027 |
Group |
During 2023, there has been a frequency index < to 7.5 and a severity index ≤ 0.2. In particular, it is recorded: |
![]() |
Contain the severity index** below 0.2 for the next 5 years
** Severity index (no. of days lost due to injuries/hoursworked x 1,000) |
Conducting work-related stress risk analysis
Descrption/Target | Timeline | Perimeter | Status | SDGs |
100% of Italian shipyards and subsidiaries over 4 years analysed on work-related stress risk |
2024 |
Italy |
|
![]() |
Support tools to improve ergonomics and reduce workloads
Description/Target | Timeline | Perimeter | Status | SDGs |
Carry out a feasibility study for the adoption of tools to support manual activities, such as industrial exoskeletons, that are compatible with the work environment on board ships under construction in relation to the increase in the average age of the working population in order to achieve an improvement in working conditions in certain activities that engage the musculoskeletal system through robotic structures of various types |
2024 |
Group |
|
![]() |
Following the outcome of feasibility studies, make the tools identified as suitable for Group companies with similar production processes progressively operational |
2027 |
Supporting inspection activities through robotic systems
Description/Target | Timeline | Perimeter | Status | SDGs |
Carry out a feasibility study for the adoption of autonomous inspection and monitoring systems for shipyard areas and on board ship. These tools will be used to perform their tasks in high-risk or difficult-to-access areas for personnel or for the automation of low value-added tasks |
2023 |
Group |
One of the strands of in-depth study initiated in 2023 relates to the adoption of Autonomous Mobile Robot (AMR) systems for inspection and monitoring at the construction site and on board ship. The feasibility study focused on assembly/construction activities, activities in hazardous areas or poorly accessible, and activities with low added value for operators. |
![]() |
Development and operation of 3 prototypes such as: quadrupeds or rovers equipped with sensors for monitoring activities, drones for inspection to analyse accessibility of high-risk areas |
2025 |
|
||
Extension of instruments to Group companies with similar production processes |
2027 |