Our goal is to ensure and maintain an excellent level of quality in every strategic decision, business processes and activity, with the ultimet aimf of achieving complete customer satisfaction.
This vision is encapsulated in our Quality Policy – A Commitment to Excellence, updated in 2024, which outlines a structured and excellence-driven approach. Through deliberate choices and integrated processes at every organizational level, we adhere to seven fundamental principles, with customer focus serving as the cornerstone guiding all others.
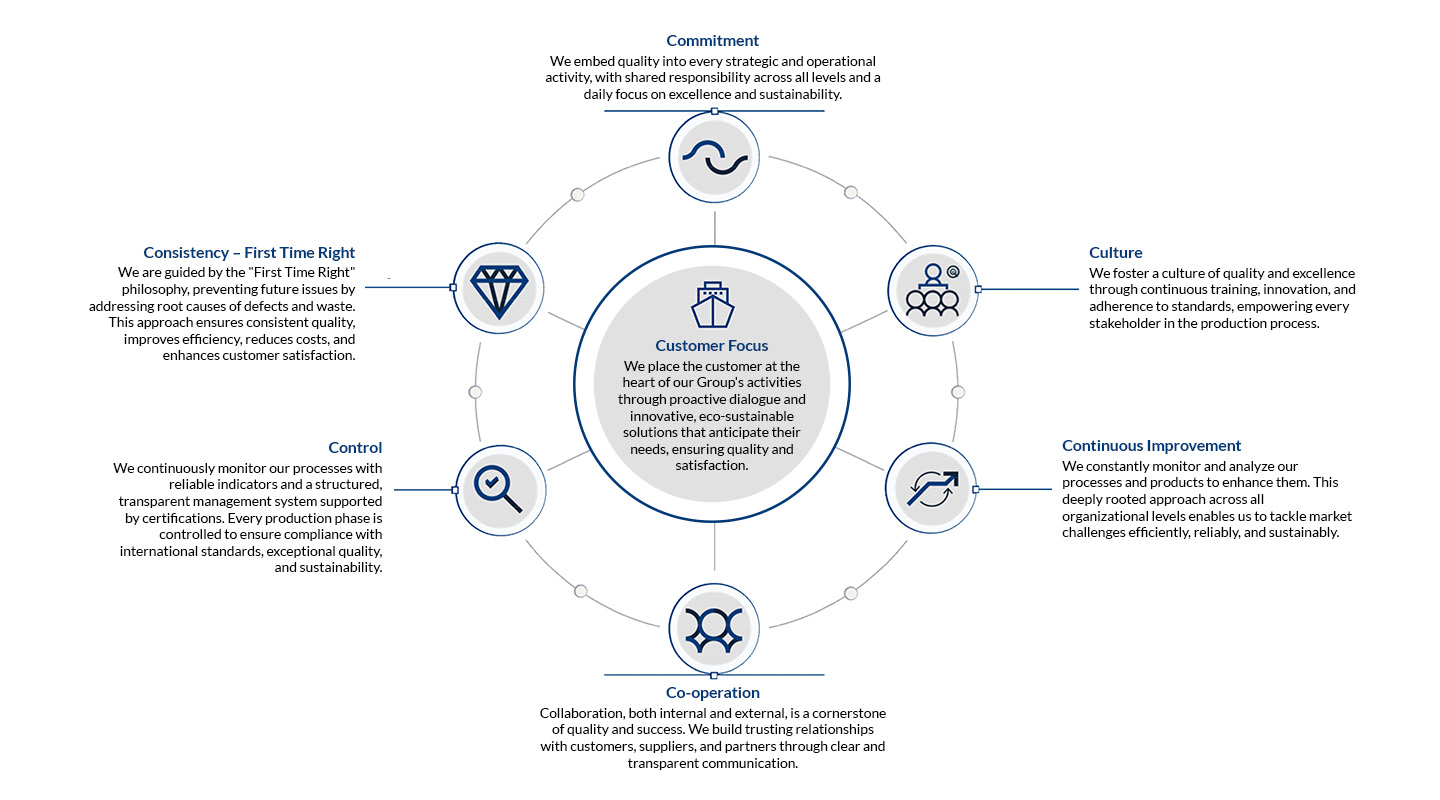
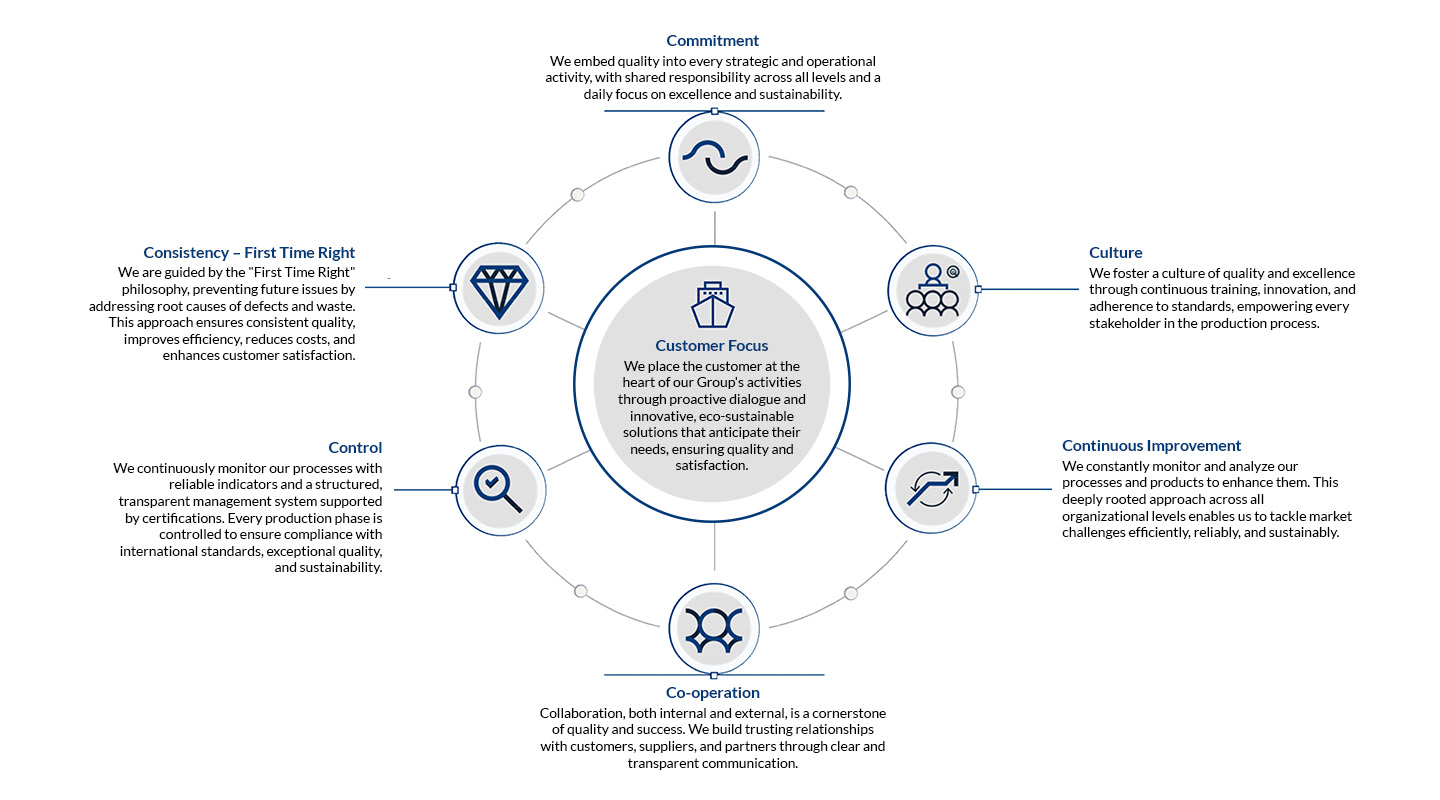
The Quality Policy underpins the ISO 9001-certified management systems adopted by Group companies at both the site and division levels, ensuring compliance with the highest standards. Currently, 100% of Italian production plants are certified ISO 9001 and 95% at Group level.
The quality system includes periodic internal audits, conducted at both the project and site levels, to monitor the correct application of procedures and ensure compliance with ISO 9001 standards. These activities foster a widespread culture of quality, reinforced by training and update sessions aimed at operational and control functions.
Quality assurance is maintained throughout every phase of the process—from contract acquisition, design, and procurement to production and service delivery. Each phase is entrusted to a dedicated process owner.
For some specific production processes, such as the welding of the hull or manufacturing special structures for infrastructures and civil works, the Castellammare di Stabia, Palermo and Sestri Ponente shipyards hold ISO 3834-22 and EN 1090-1 certifications.
In addition to these system certifications, the subsidiary Marine Interiors, a Group company specializing in the design, refitting and delivery of turnkey cabins, holds MED B product certification and MED D process certification issued by RINA. These certifications attest compliance with European Directive 2014/93/EU on Fire Protection Requirements of the Marine Equipment Directive.
Finally, Fincantieri S.p.A. and its subsidiaries Fincantieri Infrastructure, Fincantieri Nextech, Fincantieri Infrastrutture Sociali, Fincantieri Infrastructure Opere Marittime, Fincantieri SI, CETENA and SOF, maintain their SOA certification, attesting to their qualification for the execution of public works.
Quality monitoring
Our Quality Management System is also applied to job orders, whether they be naval or other products, through the Job Quality Plan (QP). The QP is a set of documents and Control Plans and governs all aspects related to quality assurance, control and monitoring that are valid for the job to which they apply. It guides the operating structures in the correct design, construction and testing of the product.
When designing and building complex products and systems, such as cruise ships, submarines or industrial diesel engines, there is always the possibility that the process may be subject to deviations from standards, design changes, unexpected events and supply or execution errors. These ‘non-quality’ events are normally detected and tracked by internal structures, by the customer's inspection staff and by the classification bodies, or more rarely after delivery, with interventions in the guarantee and after sales period. The remedial actions follow the industrial practice that involves increasing costs/times to adjust, repair, redo and replace in order to minimize the impact for the customer. The quantitative and qualitative analysis of these events, appropriately recorded and classified, gives rise to mechanisms for reviewing the projects. In the case of shipbuilding, the analyses trigger the processes of continuous improvement, in order to ensure that the same errors are not repeated in subsequent jobs. A closing report/booklet is produced, with the main lessons learned, in order to share with all the operating sites the identified countermeasures to the causes of the error and make the consequent prevention and improvement actions possible.
Which objectives do we have on this topic?
Product quality and safety: 2023-2027 Sustainability Plan objectives and targets
Continuous improvement of the quality and safety of products and services in compliance with technical standards, in all phases of the production process to meet the high standards required by the business
Discover the objectives
Increasing the level of control over the cyber risk exposure of the product supply chain
Description/Target | Timeline | Perimeter | Status | SDGs |
Activation of an audit plan on cyber risk exposure from systems belonging to a pool of 20 suppliers, representing 90% of the cruise business's cyber-critical systems as per IACS UR E26 standard
100% Italian shipyards already in possession of ISO 9001 certification |
2024 |
Fincantieri S.p.A. |
In 2024, we launched a cyber maturity assessment plan for our suppliers. The questionnaire used for these assessments was integrated into Fincantieri’s supplier registration platform, enabling the activation of the Cyber Vendor Due Diligence process. This activity was initially piloted with 20 suppliers and subsequently extended to approximately 7,000 users. Specifically, we assessed 464 suppliers, including 55 that account for 90% of the critical systems in the cruise segment from a cybersecurity perspective, in line with the IACS UR E26 requirements. |
![]() |