In our role as supply chain leader, we responsibly pursue a shared path toward sustainability, bringing our partners on board and guiding them through a process of collective growth grounded in innovation, accountability, and long-term vision.
To this end, we have defined a sustainable supply chain strategy that promotes continuous improvement across environmental, social, and governance (ESG) issues, while fostering a culture centered on development and the well-being of local communities.
At the heart of this commitment lies the Suppliers Identity, unveiled during the Fincantieri Supplier Summit held in Genoa on 17 October 2023. It sets out a framework of values to be upheld and promoted throughout the entire supply chain. This shared identity statement is a concrete expression of our principles and of our ambition to build a cohesive, responsible, and forward-looking industrial ecosystem.
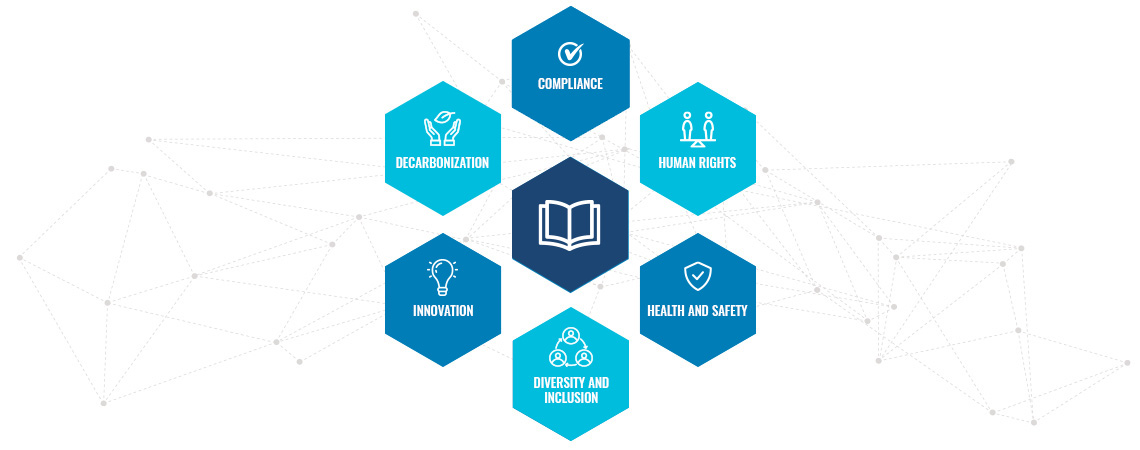
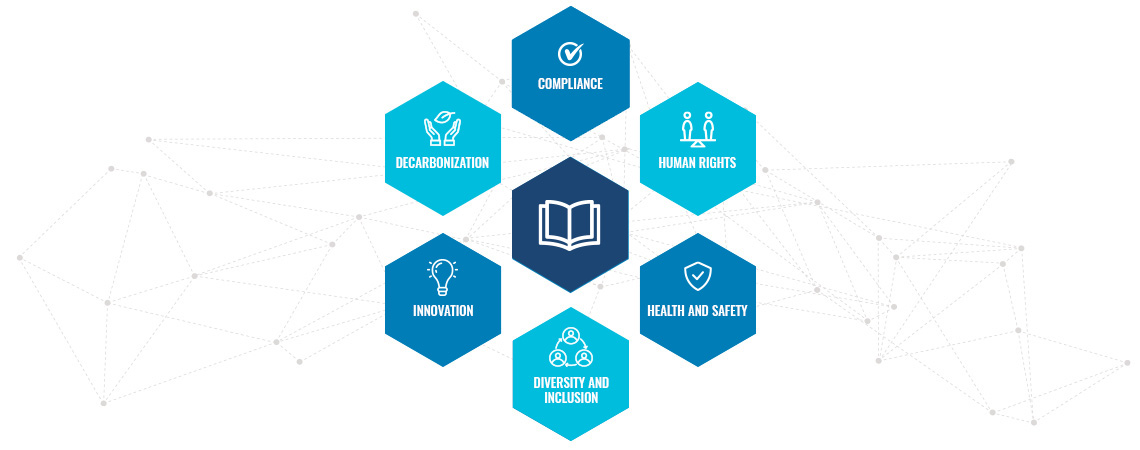
To build strong, transparent, and long-lasting relationships with our partners, we require their formal adherence to key Group policies designed to ensure the responsible management of the supply chain:
• Suppliers’ Code of Ethics
• Conflict Minerals Policy
The Suppliers’ Code of Ethics is the primary tool through which we formalize and communicate the values, principles, and responsibilities set out in our Code of Conduct, the Sustainability Commitments Charter, and the 2023–2027 Sustainability Plan. Through this document, we call on our partners to take concrete responsibility in the following areas:
• Environment – by ensuring full compliance with applicable regulations and taking measures to minimize environmental impacts, including through eco-design practices and a strong focus on product quality and safety;
• People and communities – by guaranteeing workplace health and safety, promoting decent working conditions, preventing all forms of forced and child labour, respecting freedom of association and collective bargaining, and ensuring inclusion, gender equality, protection against all forms of violence and harassment, privacy rights, and respect for local communities;
• Ethical and integrity-driven business conduct – by actively combating corruption, preventing conflicts of interest, complying with competition and anti-money laundering laws, maintaining accurate and transparent accounting records, safeguarding confidentiality and information security, and adopting ethical procurement standards across the entire value chain.
Lastly, we have adopted the Conflict Minerals Policy with the aim of promoting a supply chain free from minerals extracted, refined, or traded under conditions of armed conflict or human rights abuses, with particular attention to the Democratic Republic of the Congo and other conflict-affected or high-risk areas.
In line with this Policy, we have recently updated our Product Compliance procedure, which now requires all suppliers and contractors to formally declare that their sourcing is exclusively from smelters or refiners certified as conflict-free.
Initiatives to Drive Supply Chain Sustainability
PartnerShip
We are committed to supporting and guiding our supply chain in its sustainability journey by providing our partners with the tools needed to navigate this path of growth.
To this end, we launched PartnerShip, a supply chain programme born out of the desire to develop a sustainable ecosystem by involving the entire supply chain. PartnerShip represents a step forward in supplier engagement and aims to foster long-term relationships with our partners to jointly address and overcome the strategic challenges ahead. This marks the beginning of a sustainable development journey for the supply chain, underpinned by dialogue and shared initiatives.
PartnerShip is designed to:
• lead the ESG and Digital transition;
• empower our partners to enable collaborative growth;
• share knowledge and best practices.
Watch the video
The programme targets 1,000 strategic suppliers, selected based on their relevance to the business, their registration in the vendor list, the continuity of the commercial relationship, and the potential risks they may pose to the supply chain.
The ESG component is particularly central to PartnerShip. Among other things, it seeks to strengthen the capabilities of our partners and support them in managing risks and improving business performance.
PartnerShip is implemented through Webinars, RoadShows and the Suppliers Summit.
Webinar
In December 2023, we launched the first PartnerShip engagement initiative: a series of thematic webinars for the supply chain, focusing on key strategic areas.
The first session, “Fincantieri Supply Chain Finance”, focused on financial support tools available to our suppliers, in collaboration with leading Italian financial institutions such as CDP, Simest, SACE, and SACE FCT. The event registered participation from over 140 suppliers.
In 2024, we hosted a webinar titled “Leading Towards a Sustainable Supply Chain” to address key sustainability challenges and align suppliers with the most impactful regulatory updates. The session offered specific guidance on the Corporate Sustainability Reporting Directive (CSRD) and officially launched the ESG Journey, a continuous support and engagement path on ESG topics. The event attracted more than 180 suppliers.
Later in the year, we held a session on “Cyber Resilience in Fincantieri’s Supply Chain”, providing updates on cybersecurity regulations, aligning our suppliers with Fincantieri’s strategy and practices, and including an industry testimonial to share real-world best practices. The session received excellent feedback and was attended by over 400 participants.
RoadShow
In 2024, we held a RoadShow at the Palermo shipyard focused on ESG topics.
The event was a unique opportunity to engage our local partners in the broader supply chain journey, with the involvement of political institutions and local stakeholders. It also provided a platform to highlight the specific characteristics of the territory and its community. During the event, we shared both our strategic direction and current and future initiatives at the Palermo yard.
Suppliers Summit – “Charting New Waters”
In 2024, we hosted our annual Suppliers Summit, bringing together senior management from our strategic suppliers and key institutional stakeholders.
The event offered a platform to share updates on our Industrial Plan, recognise the value of Made in Italy and SMEs, discuss the future of the supply chain, and explore Fincantieri’s digital and sustainable transformation.
We created dedicated engagement moments for our partners, including the launch of the Fincantieri Suppliers Award, which celebrates excellence across the supply chain. Eleven best practices were recognised in three categories: Strategic Business Projects, Health & Safety, and ESG.
In the ESG category, in addition to awarding the overall top performer, we also recognised SMEs that excelled in the three ESG pillars — Environment, Social, and Governance — highlighting the quality of their sustainability journeys and the presence of high-performing, responsible businesses within our supply chain.
A special PartnerShip networking area was set up, where suppliers could meet with programme partners — companies, associations, and institutions supporting the initiative through strategic collaborations and dedicated services.
Following the Summit, we signed a Memorandum of Understanding with Simest to foster the growth and international competitiveness of businesses in the shipbuilding supply chain, promoting investments aligned with our industrial objectives.
The event was attended by more than 300 supply chain companies.
Reverse Factoring
To facilitate credit access for our suppliers, we have established a series of reverse factoring agreements with leading Italian financial institutions. These agreements allow suppliers to monetise receivables from the Parent Company and/or its main subsidiaries before their due date and under predefined conditions.
We have also transformed several of these agreements into ESG-linked reverse factoring schemes, providing immediate financial benefits to suppliers who have embarked on sustainability journeys and raising awareness across the supply chain of the importance of ESG alignment.
This tool enables access to preferential conditions based on ESG performance, fostering alignment among all stakeholders around shared sustainability goals.
Supplier management process: qualification, monitoring, evaluation and audit
We have adopted a new e-procurement portal, e-NGAGE, designed to cover the main phases of the supply chain management process: registration, qualification, invoicing, order progress status, and more.


Our digitalization process aims to simplify communication with suppliers and improve the efficiency of procurement and supply chain operations.
The management and continuous improvement of a reliable supplier base are essential to achieving our objectives, both economic and sustainability-related. For this reason, a rigorous process has been developed for the qualification and performance monitoring of strategic suppliers, based on the evaluation of economic, technical, reputational, social, and environmental aspects—particularly with regard to integrity and anti-corruption measures.
Supplier selection is critical to ensuring impartiality and equal opportunity, which are fundamental for the development and efficiency of the supply chain. For all suppliers, both during qualification and monitoring phases, particular attention is given to issues of safety, environmental protection, and the safeguarding of labor rights, with a specific focus on the ethical and reputational aspects of the suppliers.
For us, business integrity and the related principles of ethics, fairness, and professional correctness represent a constant guiding principle. We are fully aware that corporate reputation is a strategic asset to be valued and protected, so as not to compromise the trust of our stakeholders. To this end, within the qualification process, we adopt a risk-based verification model—which, for cases deemed at higher risk, includes enhanced due diligence extended also to beneficial owners—to ensure that our supply chain pursues the highest levels of compliance regarding anti-money laundering, counter-terrorism financing, international sanctions, and the most stringent standards of corruption prevention and combat, in full alignment with the company’s Anti-Corruption Policy, which is also available on the official corporate website.
We monitor the supply chain through a life cycle management approach, aimed at minimizing the environmental and social impact of a product or service throughout its entire life span. In particular, we are committed to promoting ESG principles across the entire production chain, increasingly relying on regular exchanges of information and documentation with our suppliers.
Within the supplier monitoring system, we employ a continuous performance evaluation framework (balanced scorecard) involving all relevant company functions, thereby ensuring that the required standards are consistently met over time. A supplier retains its qualified status as long as the reasons for its inclusion in the Supplier Register persist and its performance monitoring does not reveal critical issues warranting exclusion.


It is established that major criticalities are examined through a transversal, cross-functional engagement within the Supplier Observatory, a body that involves multiple corporate functions and management divisions. This Observatory oversees critical suppliers by closely monitoring identified issues, preparing detailed reports, and making consequential decisions. These may result in the development of targeted improvement plans for individual suppliers or, where necessary, the definition of timelines and procedures for the supplier’s phase-out.
With the aim of assessing our suppliers from an ESG perspective, we have launched a four-year ESG assessment program. This initiative involves 1,000 strategic Group suppliers out of the 3,950 Tier 1 suppliers operating for Fincantieri S.p.A. In 2024 alone, over 760 suppliers have already been evaluated, representing 85% of the total procurement volume from strategic suppliers.
The ESG score is assigned based on criteria defined by a working group composed of representatives from various companies within the sector and outlined in the ESG Supply Chain Guidelines, ensuring objectivity and independence. A supplier’s ESG rating is determined according to their supply categories and follows the completion of a specific questionnaire hosted on the SupplHi platform, which suppliers access via the e-NGAGE portal. The evaluation covers the three pillars: Environmental, Social, and Governance, on a scale from A (highest) to E (lowest).
These results help identify strengths and areas for improvement in sustainability performance. The presence of an ESG badge with a summarized score facilitates the sharing of evaluations with all potentially interested stakeholders. The evaluation model is periodically updated in accordance with the guidelines and the working group meetings in which Fincantieri actively participates.
The ESG evaluation of suppliers is part of a specific objective within the 2023-2027 Sustainability Plan, with its correct implementation monitored by the Board of Directors and the competent Executive Leadership.
Every year, we systematically conduct verification activities at our suppliers through various types of audits, encompassing both sustainability and qualification and monitoring assessments.
In 2024, we carried out 117 audits, of which 85 were sustainability audits. Compared to 2023, these activities have been enhanced by the introduction of a structured initial assessment phase, aimed at prioritizing suppliers for onsite visits.
The ESG audit process begins with an annual planning phase based on a structured, risk-based methodological approach. This approach takes into account a range of risk factors across the three dimensions of sustainability, geographical location, sector of activity, and strategic importance to the business. Suppliers are grouped into clusters and the scope of audits is then defined according to specific prioritization criteria, through several evaluation phases ranging from risk assessment to relevance assessment.
The audit checklist includes verification of environmental, energy, health and safety management systems, organizational models, compliance with human rights and HSE (Health, Safety and Environment) requirements, controls prescribed by Italian Legislative Decree 231/2001, chemical management (with reference to the European Regulation 1907/2006, known as REACH, and other sector regulations), as well as adherence to the principles set forth in Fincantieri’s Supplier Code of Ethics.
For each audit conducted in 2024, we received, analyzed, and evaluated a detailed report encompassing all findings, the checklist with performance levels achieved by suppliers across the three ESG areas, and a module of observations and non-conformities, which was shared and discussed with the supplier.
Following the observations reported to suppliers through this module, the evaluation process is complemented by ongoing supplier support to facilitate continuous improvement in ESG performance in line with Group criteria. Specifically, based on the findings raised by independent auditors—identified as opportunities for improvement or areas requiring reinforcement—72 improvement plans have been activated. Progress on these plans is monitored regularly through ongoing dialogue with the suppliers involved.
Furthermore, seven suppliers were found to have specific non-conformities. Fincantieri responded promptly and decisively, requesting immediate resolution. Of these, three cases were resolved within the year, with formal documentation certifying closure; for the remaining four, tailored remediation plans were developed, requiring suppliers to achieve compliance no later than the first half of 2025. It is important to note that none of the non-conformities related to violations of human rights; accordingly, no cases of significant negative impact were recorded. Nonetheless, suppliers may be excluded from contracting if they fail to achieve the minimum ESG requirements within a prescribed timeframe.
The overall results are summarized in the diagrams below, where a score of 100% represents full compliance with the expected standards.
Environmental
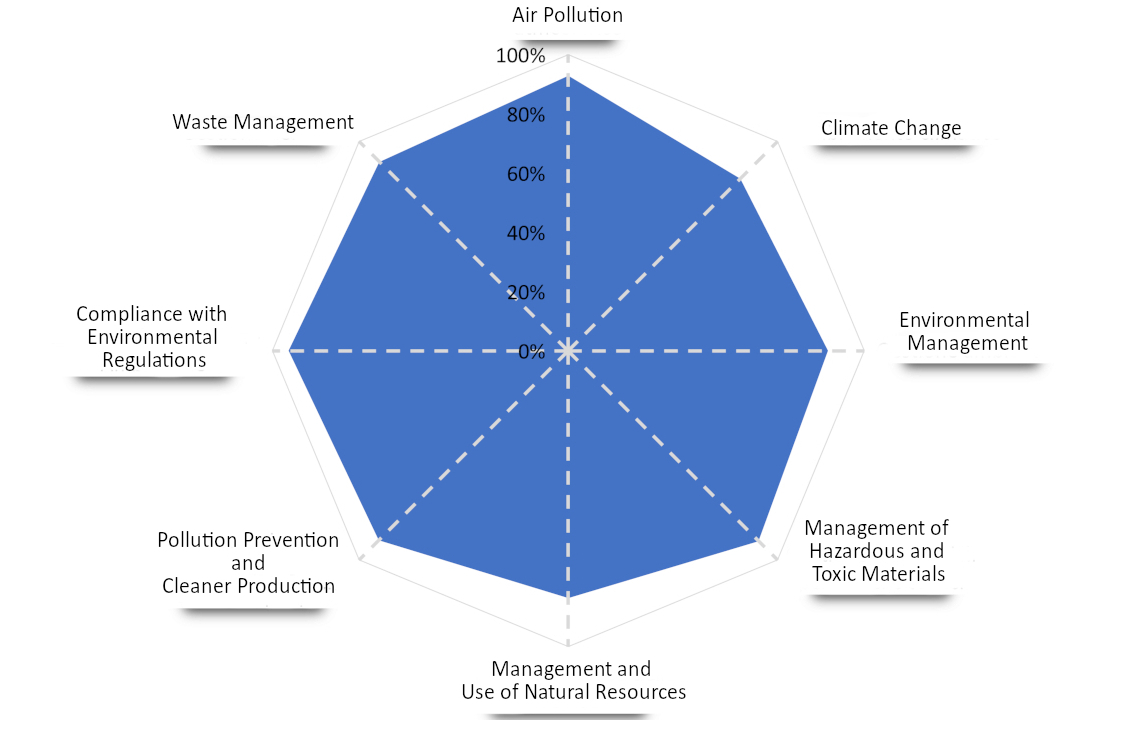
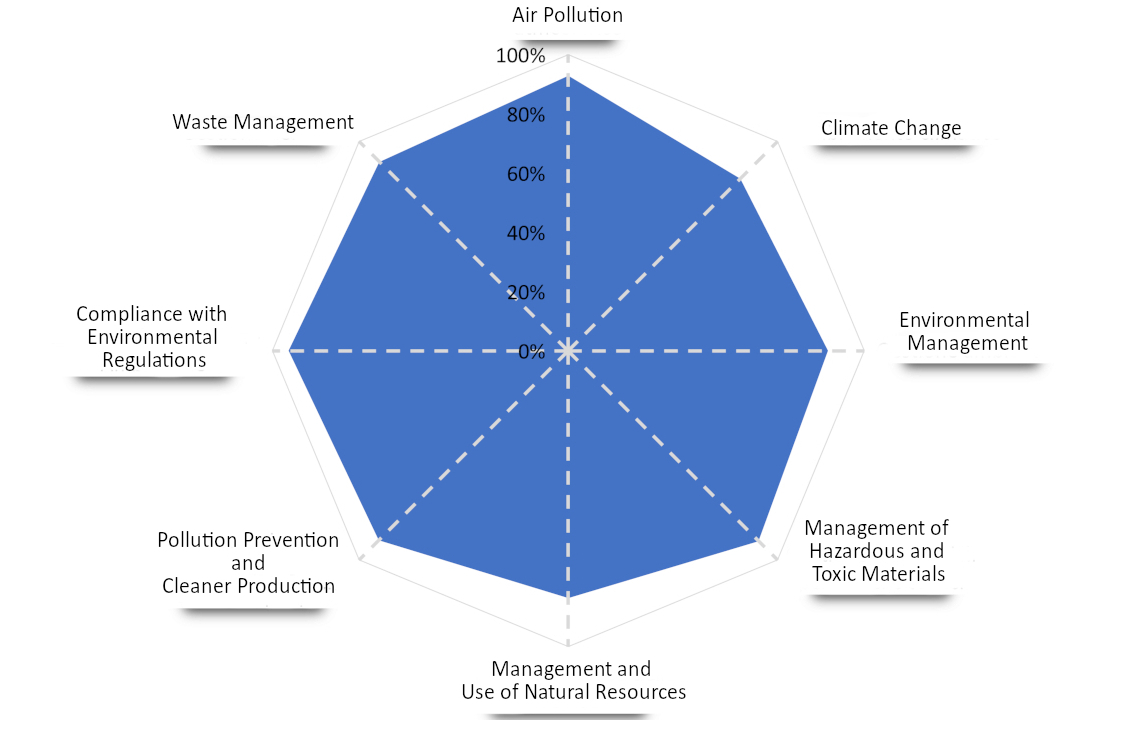
Social
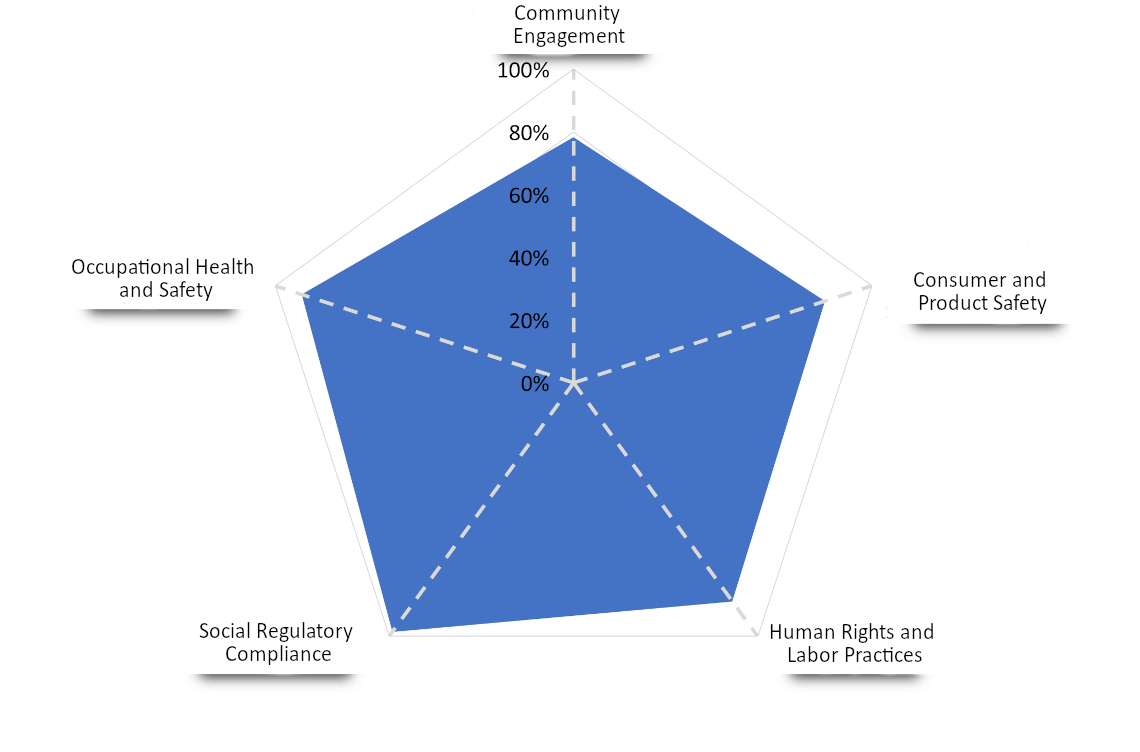
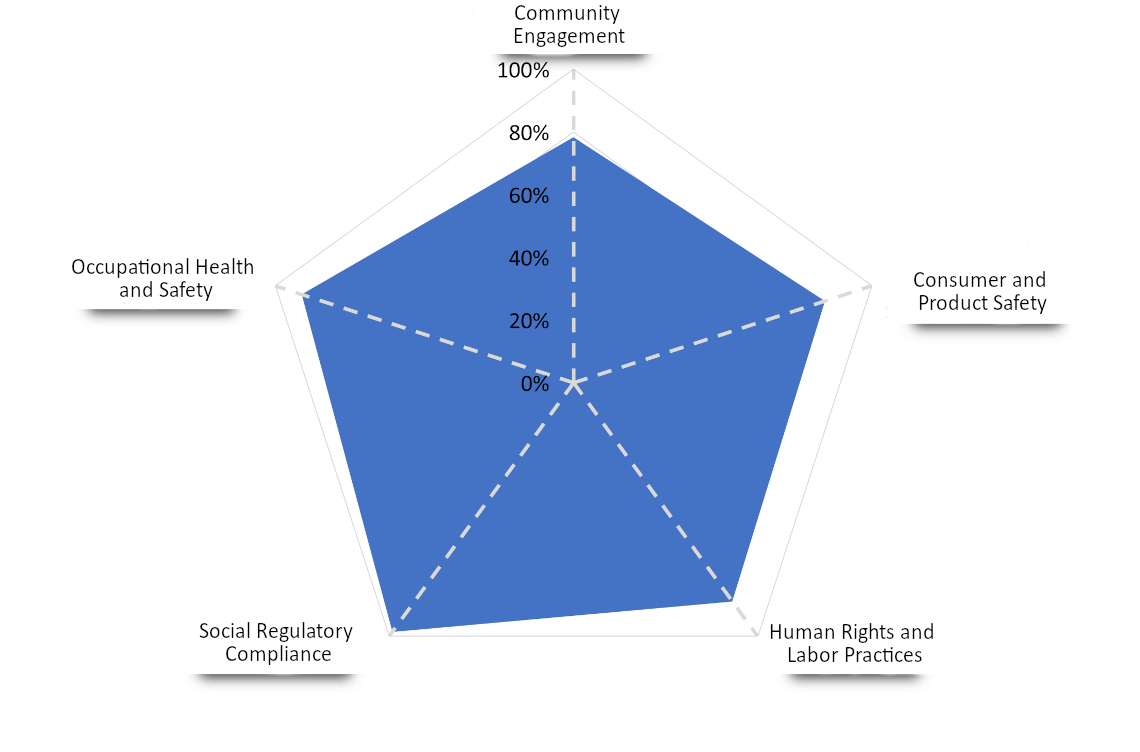
Governance
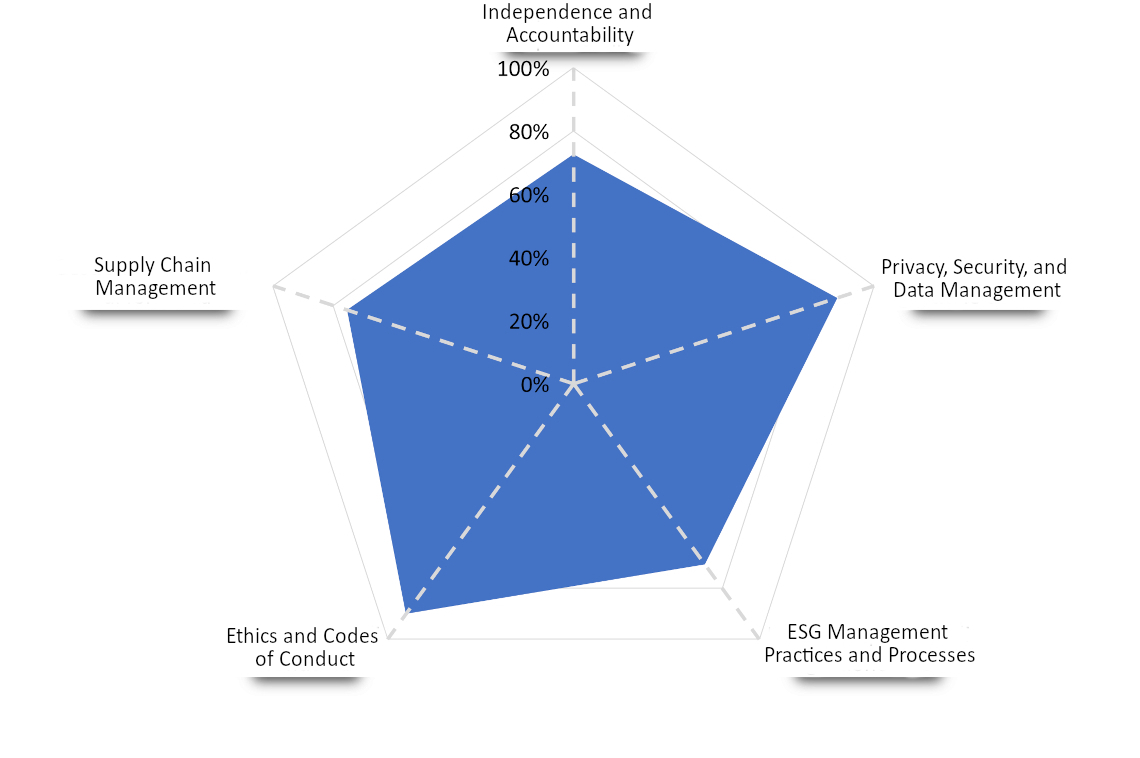
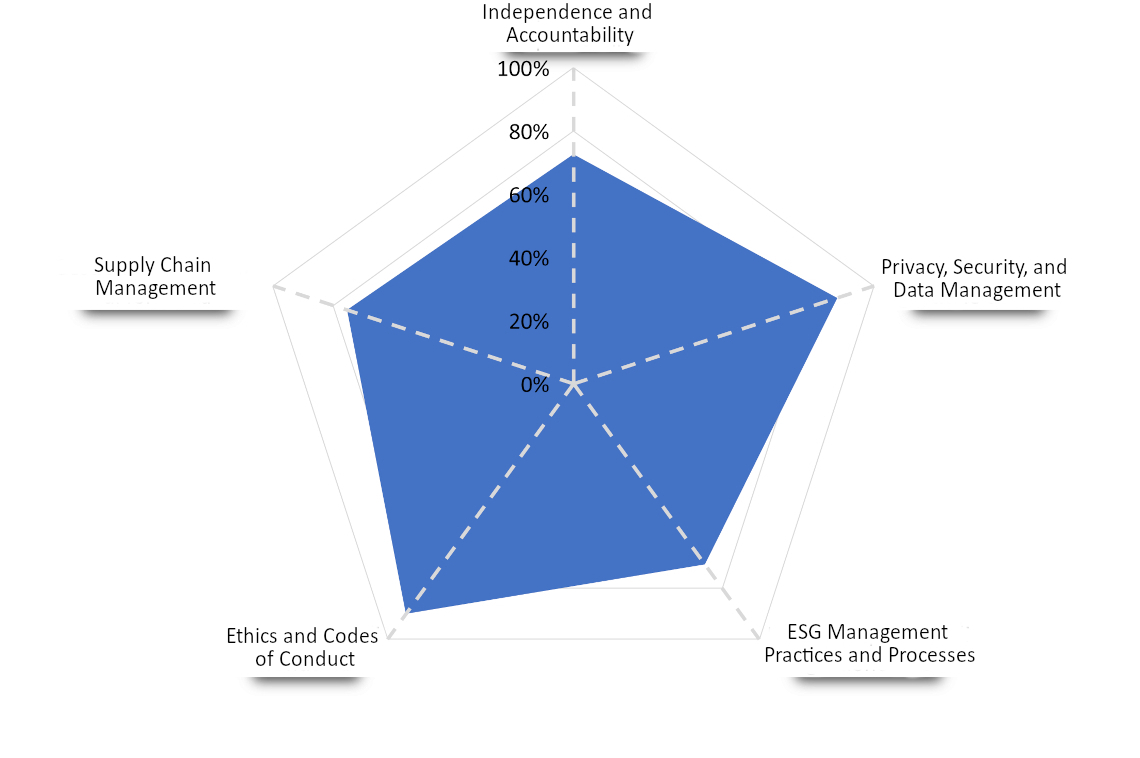
Which objectives do we have on this topic?
Sustainable Supply Chain: 2023-2027 Sustainability Plan objectives and targets
Promotion and support of a responsible and sustainable supply chain that shares our values and is based on long-lasting relationships founded on integrity, transparency and respect
Discover the objectives
Development of a Sustainable Supply Chain in order to integrate sustainability criteria into the supplier qualification system and to ensure adequate risk control
Description/Target | Timeline | Perimeter | Status | SDGs |
• Launch of an ESG assessment program and coverage of the most relevant suppliers in terms of purchasing volume of 30% |
2023 |
Group (excluding American subsidiary companies) |
At the end of 2023, suppliers accounting for 32,4% of the total perimeter purchasing volume were assessed in ESG terms, exceeding the 30% target defined in the Plan. The ESG score makes it possible to assess the supplier in terms of sustainability and at the same time provide it with a tool for analysis and improvement. |
![]() |
• Attribution of ESG scores to at least 50% of strategic qualified suppliers* |
2024 |
|
||
• ESG assessment and gap analysis on the evaluated sample |
2024 |
|||
• Attribution of ESG scores to 100% of strategic qualified suppliers |
2025 |
![]() |
||
• Extension of ESG supplier scoring system to European subsidiaries** |
2025 |
|||
• Definition of a model for the use of ESG assessment in procurement processes: |
2025 |
|||
• Implementation of reward mechanisms linked to ESG assessment |
2026 |
* Meaning suppliers in the Register, net of customer-referenced and imposed suppliers.
** The result is subject to the extension of the Fincantieri S.p.A. model to VARD (processes, systems, ERP and e-NGAGE portal).
Raising supplier awareness of ESG issues
Description/Target | Timeline | Perimeter | Status | SDGs |
• Organization of at least one engagement session on ESG issues per year with strategic suppliers |
2023-2027 |
Group (excluding American subsidiary companies) |
In 2024 were conducted two webinars, “Leading towards sustainable supply chains”, with the aim of informing suppliers of the regulatory updates with the most significant impact and understanding the key challenges to address together and "Cyber Resilience in Fincantieri's Supply Chain" completed the first PartnerShip series of webinars, which started with a session on supply chain finance. A roadshow was held at the Palermo shipyard, where ESG issues were discussed. We also held the Suppliers Summit - "Charting New Waters," which involved the Top Management of the Group's main strategic suppliers and important institutional stakeholders. |
![]() |
Managing «conflict minerals» along the supply chain
Description/Target | Timeline | Perimeter | Status | SDGs |
• Drafting and publishing a Policy on management of «conflict minerals»* |
2023 |
Group |
In 2024, we incorporated a clause on conflict minerals into the “Product Compliance Conditions.” Specifically, through the signing of Annex 3 “Product Compliance,” the supplier/contractor declares that the sourcing of minerals or metals containing tin, tantalum and niobium, tungsten, or gold (3TGs) originates exclusively from smelters or refiners certified as “conflict-free.” |
![]() |
• Identification and implementation of contractual tools for the management of «conflict minerals» |
2024 |
|||
• Extension to relevant subsidiaries with reference to EU Regulation 2017/821 |
2025 |
|||
• Monitoring of relevant product groups |
2027 |
* Refer to raw materials or minerals -tin, tantalum, tungsten and gold (the '3TGs') -from high-risk areas or areas affected by armed conflict, the trade of which can finance armed groups, fuel forced labour and other human rights violations and support corruption and money laundering.
Human Rights: 2023-2027 Sustainability Plan objectives and targets
Commitment to creating the socio-economic conditions to ensure respect for human rights throughout the value chain
Discover the objectives
In accordance with the guidelines being defined* and international best practices, proactively identify and assess potential risks and impacts related to the respect of human rights, incorporated in the policy and Code of Ethics, referred to and signed by suppliers in the general terms and conditions of the order
Description/Target | Timeline | Perimeter | Status | SDGs |
• Due-diligence on Italian and European production sites and their satellite businesses |
2023 |
Group |
In 2024, the human rights due diligence project advanced with the definition of a monitoring plan aimed at establishing a structured data collection framework and a system for the analysis and reporting of information related to the human rights identified as salient. The plan includes the identification of proactive indicators, designed to anticipate potential risks and enable the definition of targeted and effective interventions. These initiatives are expected to be implemented over the course of 2025, involving both internal stakeholders and the supply chain. |
![]() |
• Implementation of a plan of targeted interventions following due diligence |
2024 |
|||
• Monitoring compliance through the formalization of the monitoring and maintenance plan |
2025 |
* In order to anticipate the demands contained in the Proposal for a Directive of the European Parliament and of the Council on the Duty of Care of Businesses with regard to sustainability.
Annual (second party) sustainability audits by Fincantieri at suppliers’ premises to assess and monitor suppliers' compliance with human rights, health and safety and the environment
Description/Target | Timeline | Perimeter | Status | SDGs |
• Audits of the Group's suppliers of priority/ strategic interest on respect for human rights, health and safety and the environment (approx. 200 suppliers including the remaining 7 not carried out due to COVID pandemic issues) with at least 40 audits per year Starting from 2023, depending on the score obtained from the audit, recovery plans, progressive or immediate phaseouts will be defined on an ongoing basis, based on the severity, with evidence being reported in Supplier Oversight. |
2023-2027 |
Group (excluding American subsidiaries) |
In 2024, we carried out 85 on-site sustainability audits, significantly exceeding the annual target. To ensure the highest level of transparency and avoid conflicts of interest, the audits were conducted with the support of independent professionals. |
![]() |